Welding defects are imperfections that reduce the strength, durability, or appearance of a weld. These flaws can compromise the safety and performance of a welded structure, making it essential for welders to identify and prevent them effectively. For trade school students, understanding welding defects is crucial to improving skills and ensuring high-quality work.
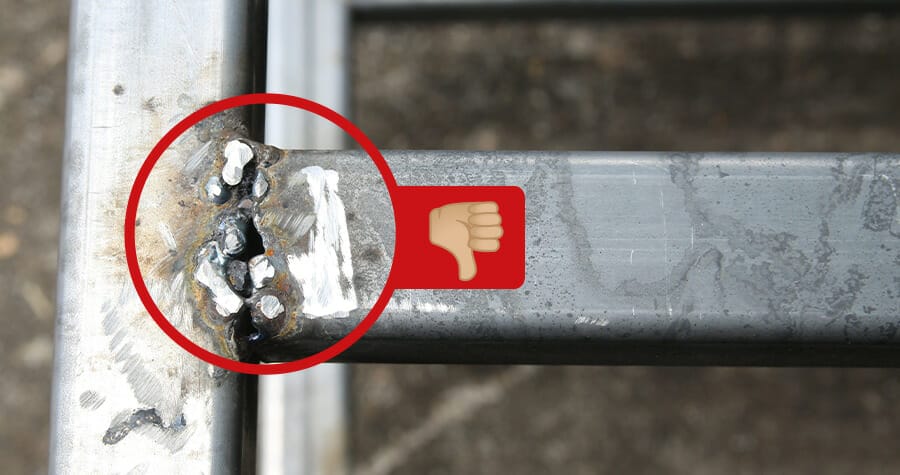
In this guide, we will explore common welding defects, their causes, and practical steps to prevent them. By learning these techniques, students can enhance their proficiency and produce professional-grade welds.
What Are Welding Defects?
Welding defects occur when the welded joint does not meet the desired specifications or standards. These defects can be external (visible on the surface) or internal (hidden within the material). Both types can lead to reduced strength, structural failure, or even hazardous situations.
Types of Welding Defects
Here are some of the most common welding defects:
- Cracks: These can appear during or after welding due to excessive stress or improper cooling. Cracks weaken the weld and can propagate over time.
- Porosity: This defect occurs when gas is trapped within the weld, creating small holes. Porosity reduces the strength and durability of the weld.
- Undercut: A groove at the edge of the weld that occurs when too much metal is melted. It compromises the weld’s strength and can lead to fractures.
- Incomplete Fusion: This happens when the base metal and filler material do not fuse properly, resulting in weak joints.
- Slag Inclusion: Non-metallic particles trapped in the weld, usually caused by improper cleaning between weld passes.
Causes of Welding Defects
Several factors can contribute to welding defects. Understanding these causes helps in taking preventative measures:
- Improper Technique: Inadequate welding skills or incorrect application of welding methods can lead to defects.
- Contaminated Materials: Dirt, grease, rust, or paint on the base metal can interfere with the welding process.
- Incorrect Machine Settings: Improper voltage, current, or travel speed can result in poor-quality welds.
- Environmental Factors: High humidity, wind, or other adverse conditions can affect the weld’s integrity.
- Material Properties: Using incompatible or low-quality materials can cause issues during welding.
How to Identify Welding Defects
Identifying welding defects requires careful inspection and testing. Here are some methods used to detect defects:
- Visual Inspection: Checking the weld’s surface for cracks, porosity, or undercut.
- Ultrasonic Testing: Using sound waves to detect internal defects such as incomplete fusion or slag inclusion.
- Radiographic Testing: X-rays or gamma rays are used to find hidden defects within the weld.
- Magnetic Particle Testing: Effective for detecting surface and near-surface defects in ferromagnetic materials.
Trade school students should practice visual inspection techniques regularly and familiarize themselves with advanced testing methods.
Preventing Welding Defects
Preventing welding defects involves following best practices and maintaining attention to detail throughout the welding process. Here are some practical steps:
- Use Clean Materials: Ensure that the base metal is free of contaminants such as grease, rust, or dirt.
- Choose the Right Electrode: Select electrodes compatible with the base metal and welding method.
- Optimize Machine Settings: Adjust voltage, current, and speed according to the material and welding technique.
- Maintain Proper Technique: Follow recommended procedures for the welding process being used, such as controlling the angle and travel speed.
- Inspect Between Weld Passes: Clean and inspect each pass to avoid slag inclusion and other issues.
Common Challenges for Beginners
For beginners, welding defects can be frustrating. Common mistakes include using excessive heat, rushing the process, or not properly preparing the base material. Overcoming these challenges requires patience, practice, and learning from experienced welders.
Trade schools often provide hands-on training to help students build confidence and develop the skills needed to avoid defects. Using welding simulators and mock projects can also enhance learning.
Why Preventing Defects Matters
Welding defects can lead to costly repairs, delays, or even safety hazards. For industries like construction and automotive, high-quality welds are essential to ensure structural integrity and reliability. By minimizing defects, welders can enhance their reputation and career prospects.
Conclusion
Understanding and preventing welding defects is a vital skill for trade school students. By learning the causes, types, and solutions for these issues, you can produce stronger and more reliable welds. Remember, attention to detail and consistent practice are the keys to becoming a skilled welder.
Start applying these tips today, and take your welding expertise to the next level!